INTRODUCING THE 3D FUSION METAL PRINTING SYSTEM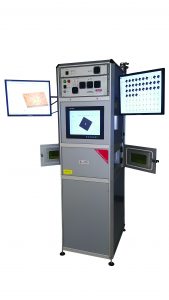
NANO POWDER DIRECT METAL SINTERING SYSTEM
Each 3D FUSION metal printing system is designed for the rapid transition of metal printed parts from prototype to production based on a common family of geometric shapes and application specific metal type. The process starts with a comprehensive review of 3D CAD files and part specifications optimizing the XYZ build-plate dimensions for minimum powder usage. Based on the part specification, the company selects the best-fit building block technologies from it BTS library of patents, licenses, proprietary metal IP and next-generation hardware representing the fastest path to MRL 10 manufacturing production readiness.
Desktop Metal printing specialist acknowledge that current generation metal printing systems manufacture metal printed parts with wide unit-to-unit variations with very few companies announcing MRL6 capabilities. Each of the company’s BTS building block technologies incrementally eliminate the system processing conditions that contribute to the wide fluctuations of metal printing parts from the same machine and from machine-to-machine.
The 3D FUSION Advantage
- Produce metal parts with complex geometries and internal structures
- Dramatically reduce product development and lead times
- Reduce molding and tooling costs
- Direct Drive Motion System—the laser head moves with the highest possible acceleration and smoothness, reducing stress and vibration on the carriage frame and lowering maintenance requirements.
- Optimized for specified powders, resulting in best performance and part consistency
- Extremely high laser positioning accuracy
- Integrated, sealed digital encoder
- Coaxial vision system and other sensors allow real-time monitoring of operation, if desired
- Optical or mechanical Z axis capability
- Double productivity option: each system can equipped with dual laser heads; each head can be configured for independent operation or Master/Slave operation